What is the recalibration trap and how to solve it
In the design of an industrial product, not all parts are destined for the same future. Most of them, in fact, will remain firmly fixed in the product, without external access, to the satisfaction of both the manufacturer and the end user.
However, a few rare components have the unfortunate necessity of periodically undergoing a specific treatment either to preserve their performance or to prove their performance. This is the case with precision environmental sensors integrated into many industrial products.
Their objective is generally to provide data necessary for the proper functioning of the product under a maximum of varied environmental conditions. For example, this is the case for the vast majority of equipment measuring gases such as EMSs (Emission Monitoring Systems) or RDE (Real Driving Emissions) measurement systems, to name just a few.
Whether due to industry-imposed normative constraints or simply to maintain performance, these sensors must periodically (typically annually) undergo a treatment that guarantees the precision and accuracy of their measurement, through recalibration, adjustment, and certification tasks.
And it is then that manufacturers are divided into two main categories: those who anticipated the need, and those who regret not having done so.
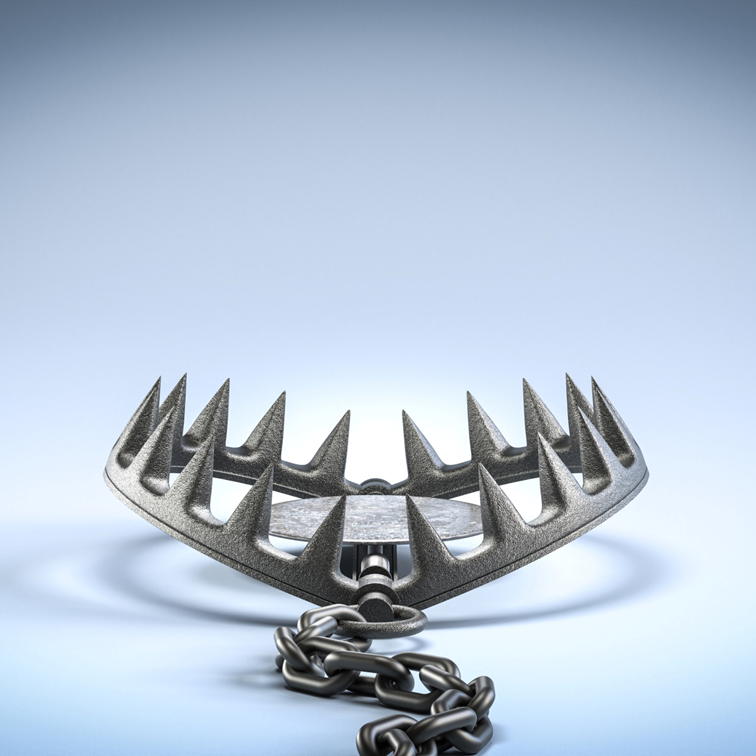
What is meant by the “recalibration trap”?
The recalibration trap is the act of neglecting, during product development, that the environmental sensors within it will need to undergo recertification and recalibration, and this, on a regular basis. This trap lies in wait for all industrial product designers targeting a highly regulated market, such as industries analyzing pollutant gas emissions, for example.
Why is it a trap?
It is quite unanimously recognized that the two ultimate criteria that determine the final selection of a sensor solution are quality (precision) and cost. However, typically, these two criteria are evaluated at the product’s manufacturing stage and not over the entire product lifecycle. Under the pretext of optimizing precision and cost, teams too often forget that maintaining this same precision in the future will also contribute to the total cost. And ultimately, from the first annual recalibration, it becomes evident that the solution initially considered a windfall turns out to be dangerously difficult to maintain.
Consult this article to better understand the implications of recalibration on costs and customer experience.
Why does calibration not solve the recalibration problem?
If calibration is considered the very first intervention performed on a sensor to guarantee and maximize its precision, this action is generally undertaken in the factory by the sensor manufacturer itself, and its mechanism is not necessarily accessible to the integrator and even less so to the end user of the product.
This is how the appeal of buying ready-to-use sensors with traceability certificates often lowers the guard of the industrial manufacturer who will mentally mark the issue of calibration and certification as “resolved”. However, regardless of whether the sensor is initially calibrated, recalibration will indeed need to take place, the following year, the next one, and the one after that, and being equipped with a pre-certified sensor does not solve the questions of 1) how the recalibration will be performed? and especially 2) who will be in charge of it?
In what context does the recalibration trap exist?
All products integrating environmental sensors operating in highly regulated industries are concerned by this reality.
Biotechnology, bio-pharmaceutical, and air quality analysis industries are particularly affected.
Products related to the testing and certification industry, whether directly or indirectly, are also heavily impacted, as they are closely monitored by very strict standards.
If you are involved in product development in these industries, taking a moment to evaluate whether the recalibration trap awaits you could save you a lot of time and money in the months, or even years, to come.
How to effectively solve the recalibration problem?
The key to the puzzle lies in these two words: modularity and accessibility.
A sensor is considered modular if it can be easily replaced by the end user. By easily, we mean the existence of a simple mechanism with no risk of error by which the sensor can be removed and exchanged without worrying about making a wrong move. A modular sensor therefore requires no screwdriver, no wiring intervention, and no data manipulation to be removed or exchanged. Modularity provides an answer to the puzzle by ensuring that the sensor can eventually be removed from the product and then reintegrated later to allow recalibration tasks.
To those who think: but why not simply calibrate on-site as we have always done? The other part of the answer, accessibility, could create a paradigm shift in your approach.
By accessibility, we mean the existence of a simple and open software that allows any ISO17025 accredited laboratory with the competence to perform the recalibration task. Accessibility to the recalibration function reduces annual recalibration costs by a factor of 5 to 10 compared to on-site recalibration. When the time comes, the modular sensor can simply be removed, placed in an envelope, shipped to the laboratory, and return a few days later in its best possible condition with its certificate.
And this, by the end user themselves, with complete autonomy. To their satisfaction and that of the product manufacturer.
And if the end user has a few spare sensors, they can perform an instant hot-swap and will experience no downtime during the operation.
Everyone wins. The end user can be agile, autonomous, suffers no downtime, and simplifies their normative documentation process. The manufacturer enjoys much better customer satisfaction, saves on customer support costs, and reduces generally extremely high maintenance costs.
Examples of Dracal Modular All-in-One Sensors for Easy Recalibration
How Dracal solves the problem for you
First, Dracal’s precision environmental sensors are modular through their USB connectivity. If there’s one point everyone agrees on, it’s that USB technology is robust, has proven itself, is here to stay, and allows perfect modularity by design. You plug and unplug without fear of making a wrong move. Each sensor is equipped with a unique serial number, enabling traceability.
Next, Dracal satisfies the accessibility criterion by offering free and easy-to-use software for visualization, recording, and easy data adjustment*. All ISO17025 accredited laboratories with the required calibration capabilities for a sensor and possessing a computer (Windows, Mac OS, or Linux) with a USB port are valid candidates for recalibrating our products. If an adjustment occurs, it is recorded directly in the sensor and follows it until the next recalibration. No external manipulation is required: the product returns recalibrated, adjusted, and accompanied by its calibration certificate.
Dracal’s Little Extra: For integrators, simplified integration tools and copy-paste code examples allow programmers of all levels to contribute to data integration. Moreover, the COM protocol communication option (VCP option) enables integration without dependence on third-party software, eliminating licensing and future update management headaches.
The solution is doubly simple. But incredibly effective. We invite you to consult the following case study to see the power of the paradigm shift hidden behind the adoption of Dracal’s modular sensor solution.
*Only Dracal instruments with the -CAL suffix are adjustable.
Next steps with the Dracal solution
If our solution interests you, and you want to know where to start, here is a simple action plan that will allow you to quickly evaluate our solution and determine if it meets your needs.
1 – Purchase one of our sensors by choosing a model option with the “-CAL” suffix (e.g., USB-PTH450-CAL). If integration based on the COM protocol is desired to eliminate any dependency on third-party software, the option also equipped with the “VCP-” suffix is the one you need (e.g., VCP-PTH450-CAL).
2 – Download DracalView. Even for users of the “VCP” option, the software will allow you to quickly view data and test the user recalibration function.
3 – Determine your integration mode. Via our command-line tools or VCP mode? Which language? Then refer to our code example bank to copy-paste the one that applies to you.
4 – Upon receiving the instrument, test DracalView, test your code example. Adapt it to your specific use case. And that’s it, it’s already done. As stated by one of our clients in this case study, yes, the sensors can be “fully integrated into [your] codebase in about 20 minutes, end to end“.
You may still have a multitude of questions. Do not hesitate to contact us to obtain answers and help with your decision-making.
Not sure if your project will benefit from Dracal’s solution?
Contact us, tell us about your project, and we’ll quickly determine if there’s a fit.
"*" indicates required fields
Conclusion
The recalibration trap is real and affects many manufacturers who still consider it “normal” to have to travel to customers annually to perform on-site recalibration tasks. Considering a solution of modular and accessible sensors will allow any team working on a new product to intervene now to counter the recalibration trap. As for manufacturers with products already deployed in the field, we hope that the case study with AVL above has convinced you that it is not too late to make an innovative change in your next model in this direction. And if you are considering using the Dracal solution, this change could happen at a speed and development cost that might surprise you and create, here too, a paradigm shift!
Always offered at no extra charge with our products!
EASY TO USE IN YOUR OWN SYSTEM
- Ready-to-use, accurate and robust real-time data flow
- Choose the interface that works best for you (CLI, virtual COM, REST API)
- Code samples available in 10+ programming languages (Python, C/C++, C#, Java, Node, .Net, etc.)
- Operates under Windows, Mac OS X and Linux
- Usable with LabView (CLI guide, Virtual COM guide)
- All tools packaged within one simple, free of charge, DracalView download
FREE DATA VISUALIZATION, LOGGING AND CALIBRATION SOFTWARE
- Get up-and-running in less than 3 minutes
- Operates under Windows, Mac OS X and Linux
- Real-time on-screen graphing and logging
- Log interval down to 0.5 second and configurable units (°C, °F, K…)
- Simultaneous use of unlimited Dracal sensors supported
- Simple user-calibration (products with the -CAL option)
- Connectivity with SensGate Wi-Fi/Ethernet gateway
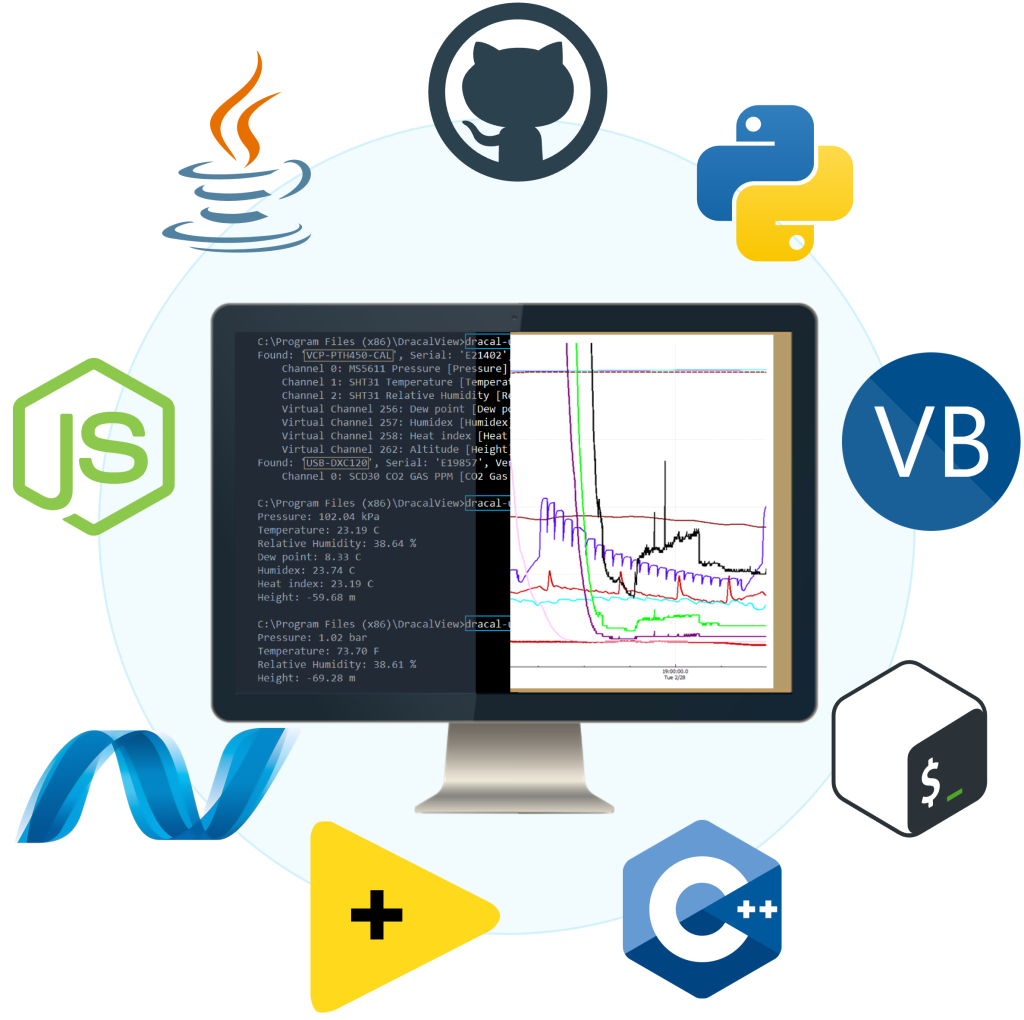
PRODUCTS YOU CAN TRUST
Approved by engineers, scientists and researchers around the world.
Thousands of companies trust our products worldwide:
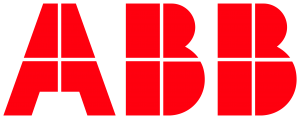
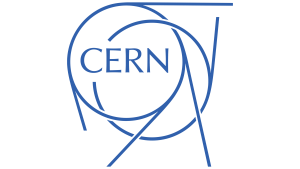
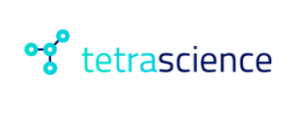
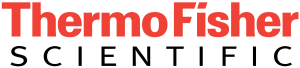
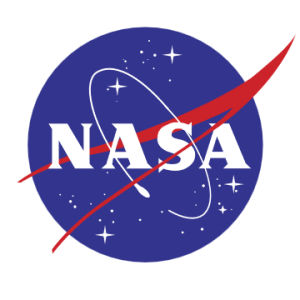
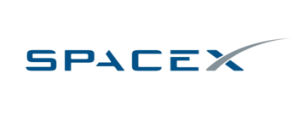
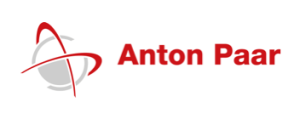
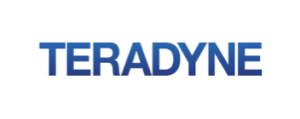
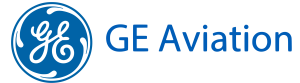
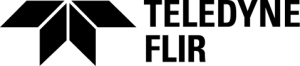
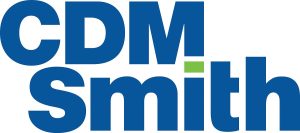
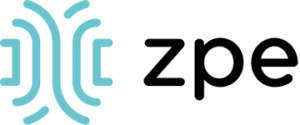